

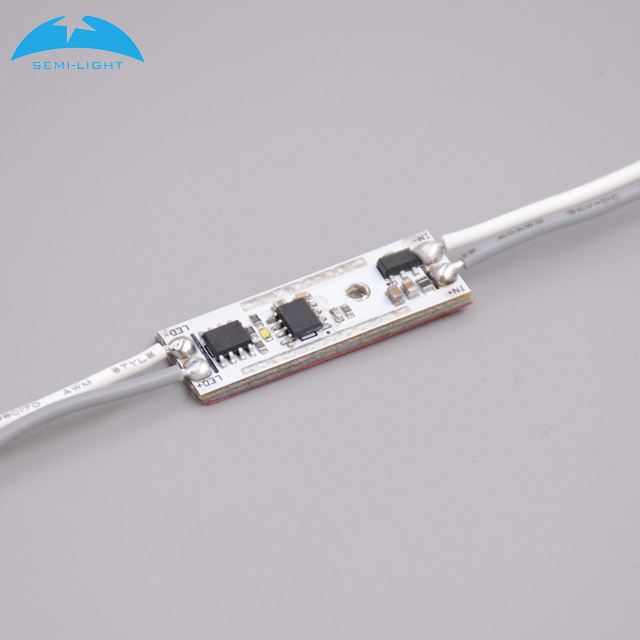
Inductive sensors are typically rated by frequency, or on/off cycles per second. Output is read by an external control unit such as a PLC, motion controller or smart drive that converts the sensor’s “on” and “off” states into usable information. With normally closed sensors, the output is an “off” signal when a target is present. If the sensor has a normally open configuration, its output is an “on” signal when the target enters the sensing zone. When the target finally moves out of the sensor’s range, the circuit begins to oscillate again and the Schmitt trigger returns the sensor to its previous output. (This is the “Eddy Current Killed Oscillator,” or ECKO, principle.) The Schmitt trigger responds to these amplitude changes and adjusts the sensor’s output.
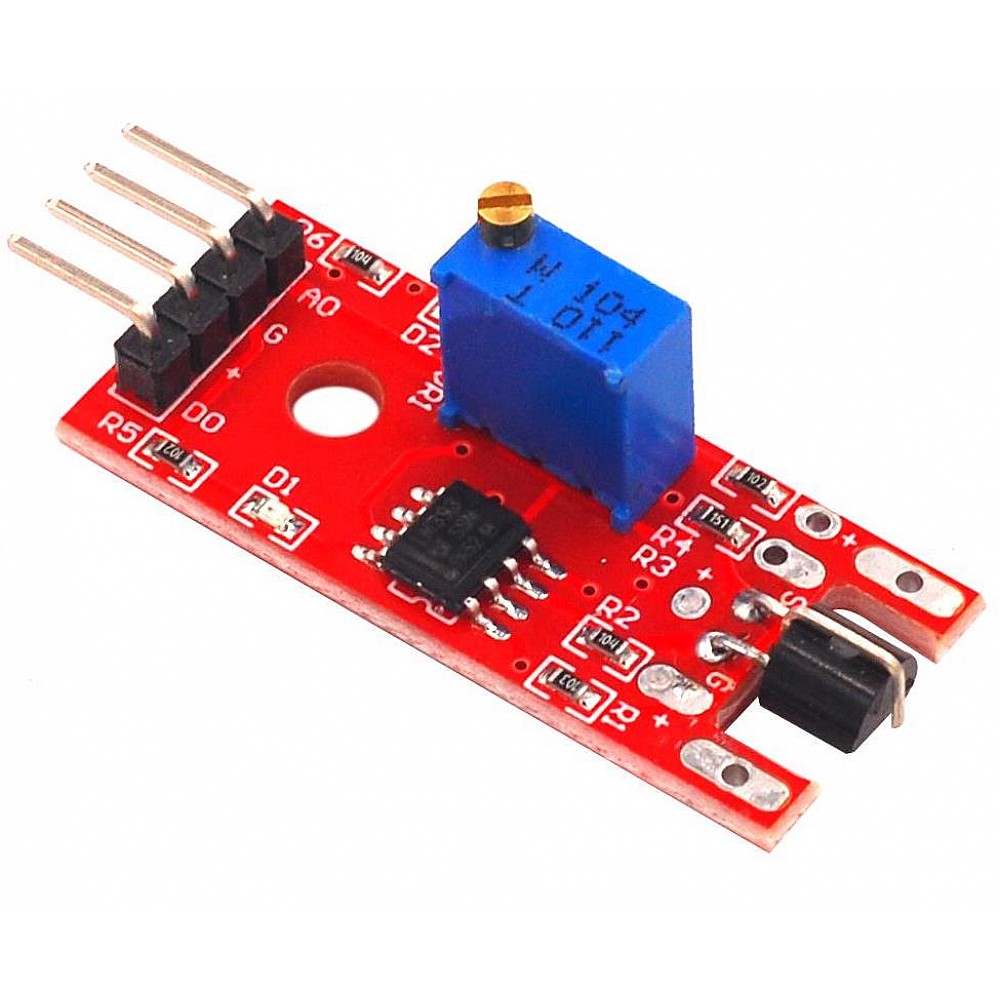
As more metal enters the sensing field, the oscillation amplitude shrinks, and eventually collapses. When a metal target enters this magnetic field, small electrical currents (eddy currents) induced on the metal’s surface change the reluctance (natural frequency) of the magnetic circuit, which in turn reduces the oscillation amplitude. The oscillator creates a symmetrical, oscillating magnetic field that radiates from the ferrite core and coil array at the face of the sensor. They are housed in enclosures typically made of nickel-plated brass, stainless steel or PBT plastic. They consist of four major components: a ferrite core with coils, an oscillator, a Schmitt trigger and an output amplifier. Inductive sensors are non-contact proximity sensors that detect ferrous targets, ideally ones made of mild steel thicker than one millimeter. Here’s a look at the most popular proximity-sensing technologies. There are many types, each suited to specific applications and environments. Proximity sensors detect the presence or absence of objects using electromagnetic fields, light and sound. Sensor Sense: Inductive position-measuring sensorsĪ Primer on Sensors for Machine AutomationĪdvances in Motion Sensors Lead to Smart Motion
